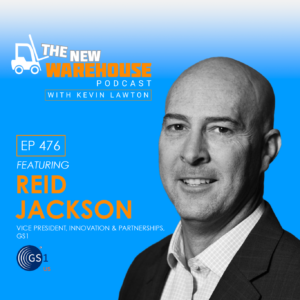
Episode 475: The Pivotal Role of Barcodes in Supply Chain Management with GS1
Barcodes are often underrated and underappreciated, but they play a pivotal role in product safety, efficiency, and movement within the
Barcodes are often underrated and underappreciated, but they play a pivotal role in product safety, efficiency, and movement within the
DuraLabel has announced the immediate availability of its new Kodiak Max, industrial sign and label print systems. Kodiak Max allows
Affordable protection that fits and feels great When eyewear fits right, feels good, and looks great, the protection stays on.
Forklift operators who are insufficiently aware of the load they are lifting and the risks that come with exceeding the
Workplace safety and health became national news 113 years ago next week when the Triangle Shirtwaist Factory fire in New York City
The American Society of Safety Professionals (ASSP) is seeking a diverse group of occupational safety and health professionals to join
BenchPlus™ Manual Leak Testing System is ideal for off-line, supplemental testing, random sampling, R&D for new container development, and select
Appleton Baymaster and Areamaster now equipped with new energy-saving dimming option, warm color temperatures Emerson is upgrading two flagships of
The American Society of Safety Professionals (ASSP) has published the concurrent sessions lined up for its signature workplace safety education event this
Attendees can experience the ELOshield forklift safety and pedestrian detection system, the new ELOshield module for automated guided vehicles/autonomous mobile
Diversified Fall Protection (DFP), a fall protection integrator in the U.S. for regulatory-driven systems and services, has announced the appointment
The Alliance for Innovation and Infrastructure (Aii) has named Timothy P. Butters to its Board of Directors. Butters, a senior
New for Spring ‘24, KEEN Utility’s Arvada Shift is designed for jobs requiring constant movement and long hours on your
Facilities provide port-wide protection as part of a $109 million safety program Officials today dedicated two new Port of Long
Link’s family of LB20 ramps are now 25 pounds lighter, feature pull-style, gas-spring-assist lifting mechanisms, stow at an 8-inch vertical depth, ship
Confidential and complimentary, new GHS L.A.B.E.L. Profile helps companies labeling hazardous chemicals follow compliance best practices. Reliance Label Solutions, which
National Ladder Safety Month is observed next month, as it is every March. Begun by the American Ladder Safety Institute
Vector Security Networks to exhibit at Manifest 2024, an expo that brings together leaders and innovators in supply chain and
From KEEN Utility for Spring ‘24, the Kenton is a retro-inspired work sneaker reinvented with lightweight protection for all-day workflow.
Dialight, a hazardous and industrial LED lighting innovation, has announced an all-new battery back-up model for its iconic LED High Bay. These