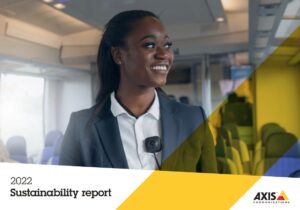
Axis Communications optimizes production to conquer Supply Chain constraints
Video surveillance industry leader ships record level of products through May 31 and continues an aggressive growth trajectory Axis Communications,
Video surveillance industry leader ships record level of products through May 31 and continues an aggressive growth trajectory Axis Communications,
Mitsubishi Logisnext Americas group (Logisnext), a North American provider and manufacturer of material handling and innovative automation and fleet solutions,
Forklifts are an indispensable and versatile means of turning, transporting, storing, or collecting goods. By mounting RAVAS weighing systems on the
Industrial Truck Association’s June 13 event emphasizes safety training and practices The 10th Anniversary of National Forklift Safety Day will
With this month’s issue we are putting the spotlight on safety, it is a good time to discuss some products,
Forklifts are an everyday essential in material handling operations, which is why forklift safety is a top priority in the
Registration is open for the fall session of SafetyFOCUS, the semi-annual in-depth education experience from the American Society of Safety
Safety in the workplace is a goal offering numerous benefits. From aiding in worker retention and meeting standards to ensuring
ARPM recognizes group for Best Safety Practices U.S.-based manufacturer Marsh Bellofram is being recognized for its commitment to safety in
The American Society of Safety Professionals (ASSP) will again welcome Doug Parker, assistant secretary of labor for occupational safety and
ELOKON Inc. has announced the appointment of Mark Stanton as its new Senior Vice President of Sales. Mark brings with
Robust and durable housings stand up to intense vibration, harsh conditions Uniform illumination improves visibility, reduces shadows The range includes
APS Resource announces the introduction of its newest innovation, the Vertical Aerial Safety Light which provides an extra layer of
The American Society of Safety Professionals (ASSP) has unveiled a plenary session that will join two general sessions in a
The American Society of Safety Professionals (ASSP) is bestowing the honor of Fellow on three members who have made significant
John Deere has deployed multiple MATE-XT exoskeletons to further facilitate better ergonomic sustainability for its employees The wearable robotic device
The revolutionary AR-glasses connect Cimcorp’s customers to the Success Services team for fast, efficient, and secure virtual support Cimcorp, a
Upgraded motor protection analyzer measures, analyzes, and reports critical performance information The automation experts at ATC Diversified Electronics, a maker of
Warehouse workers have a demanding job that requires constant material handling and operation of machinery. To ensure their safety, workers
The American Society of Safety Professionals (ASSP) has named Subba Rao Palagummi, CSP, CMIOSH, F.S. Eng., its 2023 Safety Professional of