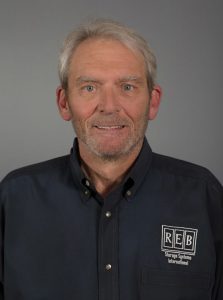
Industry leader Mike Baily remembered
Mike Baily, an Industry Specialist at REB, has passed away. A tribute was published on LinkedIn, expressing heartfelt messages about
Mike Baily, an Industry Specialist at REB, has passed away. A tribute was published on LinkedIn, expressing heartfelt messages about
stow announced the successful completion of the largest mobile racking installation in Northern Europe, at Frigoscandia’s state-of-the-art logistics facility in
The New Warehouse Podcast episode features Christian Rognes, the Chief Product Officer at Element Logic. Element Logic is the first
30-Year Global Supply Chain Executive at Fortune 500 Consumer Brands to Advance Company’s New Strategic Growth Initiatives Flux Power Holdings,
New Age Industrial has announced the promotion of Scott Schrum to Assistant National Sales Manager of the Material Handling Division.
UNEX Manufacturing, Inc. will be showcasing its dynamic solutions for manufacturing, fulfillment, retail, and logistics in Booth #S3527 at ProMat,
Material Handling Product News (MHPN) has named ORBIS® Corporation — an international provider in reusable packaging — a 2022 Readers’ Choice Product
TA Services, a premier full-service logistics provider, announces that it has been named one of the winners of Food Logistics‘ 2022 Top
The Storage Solutions Inc. (SSI) Board of Directors has officially approved the acquisition of California-based SNC Solutions (SNC). The purchase
Storage Solutions just announced forming a new partnership with Vecna Robotics, which will feature Storage Solutions as a certified integrator
Storage Solutions Inc. announces a new partnership with HAI Robotics, a next-gen warehouse automation solutions company specializing in autonomous each
Storage Solutions Inc. announces forming a partnership with Daifuku North America in which Storage Solutions has become an official integrator
Storage Solutions Inc. (SSI) announces that current President/CEO Kevin Rowles will transition to focus solely on his role as CEO
Company earns award for commitment to long-term sustainability goals ORBIS® Corporation, an international provider of reusable packaging, has been named
Designed with growing businesses in mind, Strongbox Mezzanine systems are customized to enhance durability and maximize efficiency Specialized Storage Solutions,
Selecting the right storage system can be a complicated process. Not only are there different options for every unique application,