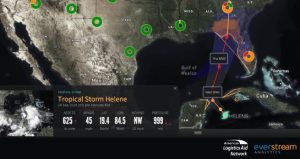
ALAN Tropical Storm Helene Situation report
As Tropical Storm/Hurricane Helene approaches landfall on the Florida Gulf Coast, ALAN is busy preparing, and we are encouraging all
As Tropical Storm/Hurricane Helene approaches landfall on the Florida Gulf Coast, ALAN is busy preparing, and we are encouraging all
China to US container leasing rates drop by 35% Average container trading prices in China decreased for the second consecutive
In a highly anticipated move, Federal Reserve Chair Jerome Powell announced the target rate would be cut 50 basis points,
Today, the NRF Foundation launched a new Customer Conflict De-escalation training program for front-line retail employees. The latest offering is part
Occupational safety and health professionals can now find even more value in being a member of the American Society of
The prospect is not waiting by the phone for your call. Most people have what you’re selling and are doing
As the material handling industry evolves and grows, so do the ranks of professionals within the business. This month, Material
Industrial SalesLeads released the August 2024 results for the new planned capital project spending report for the Industrial Manufacturing industry.
Another year-end is approaching. But I’m not sure what to expect for next year. Before we do anything further, I
ProMach has announced the launch of their Wine & Spirits Solutions group that will provide a complete portfolio of process, equipment,
Join Queen City Robotics Alliance and NASA as We Discover “The Sun Touches Everything” As we announced last month, Queen
KION Group establishes a research hub for AI-assisted intralogistics solutions Sebastian Peitz was appointed professor at the Department of Computer
ALAN has been improving logistics response to disasters for 19 years, and the need is greater now than ever. Please
GEODIS has announced plans to hire 3,700 seasonal workers across its campuses in the U.S. and Canada to help manage
Orders of manufacturing technology, measured by the U.S. Manufacturing Technology Orders report published by AMT, totaled $321.7 million in July
Ladder Safety Month: American Ladder Institute offers sponsorships for 2025 campaign This past March, the message of National Ladder Safety Month reached
As Tropical Storm/Hurricane Francine intensifies and approaches the Gulf coast, the American Logistics Aid Network (ALAN) is urging area residents
Free Online Webinar at 2:00 PM ET on Thursday, September 12, 2024 AutoScheduler.AI has announced the company is sponsoring a
The Bureau of Labor Statistics (BLS) recently released the 2024 Preliminary Benchmark Revision of the Current Employment Statistics (CES), revealing
Growth is INCREASING AT AN INCREASING RATE for Inventory Levels, Inventory Costs, Warehousing Capacity, Warehousing Prices, Transportation Capacity, and Transportation