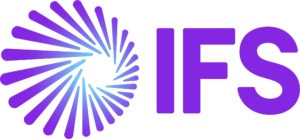
Research into AI adoption finds U.S. service companies held back by lack of skills, security concerns, and legacy systems
However, there is optimism that Industrial AI will improve quality control and bring new sustainability gains Research from IFS, a technology