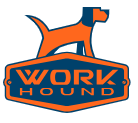
Workhound’s annual feedback trends report highlights State of Trucking in 2024
WorkHound, an employee feedback management for frontline workforce industries, unveiled its eagerly anticipated Annual Trends Report focused on top feedback
WorkHound, an employee feedback management for frontline workforce industries, unveiled its eagerly anticipated Annual Trends Report focused on top feedback
Join CVG at MODEX 2024 for an insightful seminar on “Contract Manufacturing Benefits to Your Process.” Hosted by Terry Shaw
Trew, LLC has introduced its Technology and Education Center (TEC). Located in the company’s Fairfield facility, the TEC serves as
Mid America Paper Recycling, an independent brokers, processors, and exporters of recovered paper in the Central United Sates, will exhibit
We ask questions all the time. At work, at home, amongst friends. Often, we ask questions that we already know the
In this episode of The New Warehouse Podcast, Dennis Hoang, COO and Co-Founder of Patturn, delves into the innovative world
Next year, The ARA Show™ will head back to Las Vegas and the Las Vegas Convention Center. A full day
The February 2024 BLS jobs report showed a surge of 353,000 jobs added in January, more than double than what
December 2023 U.S. cutting tool consumption totaled $187.9 million, according to the U.S. Cutting Tool Institute (USCTI) and AMT –
Research by SalesLeads’ experienced industrial market research team, shows 369 new planned industrial projects tracked during the month of January.
SalesLeads has announced the January 2024 results for the new planned capital project spending report for the Food and Beverage
Connections. Innovations. Solutions. As the speed of the manufacturing and supply chain world continues to accelerate, building a more agile,
Sometimes salespeople get a bad rap. Sometimes they create it. Sales require self-confidence but there’s a fine line between self-confidence
Trelleborg Tires will showcase its full premium portfolio for material handling and logistics at LogiMAT 2024, the international trade fair
In an upside surprise, December 2023 orders of manufacturing technology totaled $491 million, up nearly 22% from November 2023, and
SalesLeads has announced the January 2024 results for the new planned capital project spending report for the Distribution and Supply
SalesLeads has announced the January 2024 results for the new planned capital project spending report for the Industrial Manufacturing industry.
Attendees are looking to invest in automation, robotics, and tech solutions to improve the speed and resiliency of their supply
MHI has released the list of finalists for the 2024 MHI Innovation Awards. After receiving 192 submissions for this year’s
The fifth Global Lifting Awareness Day — #GLAD2024 — will take place on Thursday 18 July, represented by a new