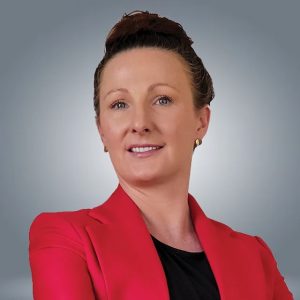
A Data-Driven approach to safety in Yard Operations: Minimizing Risk, Maximizing Efficiency
In high-volume yard operations, safety isn’t just a priority. It’s a critical responsibility. The yard is a dynamic environment where
In high-volume yard operations, safety isn’t just a priority. It’s a critical responsibility. The yard is a dynamic environment where
Launches Safety Ambassador program for companies to promote training achievements Another National Ladder Safety Month has ended with millions reminded,
The American Logistics Aid Network (ALAN) today announced the following additions to its board of directors: Marc Blubaugh, Partner and
Industry leaders to discuss how enterprise shippers are transforming yard operations into a competitive advantage YMX Logistics has announced an educational
Annual awards honor extraordinary supply chain relief efforts The American Logistics Aid Network (ALAN) has opened nominations for its ninth
With more than $200,000 raised to date toward its $325,000 goal, the PTDA Foundation is making strong strides in its
The Material Handling Equipment Distributors Association (MHEDA) successfully concluded its 2025 Annual Convention & Exhibitor Showcase, held April 26–30 in
This week saw a landmark celebration at Combilift’s global headquarters in Monaghan, marking the 10th anniversary of the highly successful
Ibukun Awolusi, Ph.D., a widely respected educator in the environmental health and safety field and member of the American Society
Order intake increases to € 2.706 billion (Q1 2024: € 2.439 billion) Revenue slightly down to € 2.788 billion (Q1
First Quarter 2025 Highlights Record equipment rental revenue of $739 million, an increase of 3% Record total revenues of $861
Many businesses and workers share a global cautiousness about automation. Yet the reality of robotics and autonomous solutions, such as
The time for systems of selling has passed. The time for sales manipulation has passed. The time for “finding the
Our financial world seems out of whack and will probably continue to be for the rest of the year. This
Industrial SalesLeads announced the March 2025 results for the new planned capital project spending report for the Industrial Manufacturing industry.
How PepsiCo uses AI and optimization to evolve warehouse decision-making AI and Orchestration Drive More Efficient Warehouse Execution AutoScheduler.AI has
The American Welding Society (AWS) has announced the highly anticipated Welding Summit 2025, to be held August 6-8, 2025, at
As fleets seek sustainable energy solutions, propane delivers 99% reduction in NOx alongside increased reliability This Earth Day, the Propane
The American Society of Safety Professionals (ASSP) encourages safety professionals and employers to raise awareness and participate in the 12th
The latest round of tariffs introduced by US President Donald Trump is set to create significant disruptions in global supply