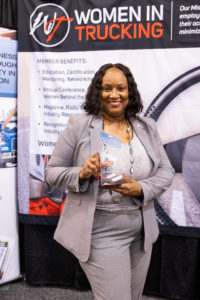
Women In Trucking Association names Trina Norman of UPS as 2022 Influential Woman in Trucking
The Women In Trucking Association (WIT) presented Trina Norman, Southern California Feeder Operations Manager, UPS, with the 2022 Influential Woman in
The Women In Trucking Association (WIT) presented Trina Norman, Southern California Feeder Operations Manager, UPS, with the 2022 Influential Woman in
The Women In Trucking Association (WIT) awarded Walmart the inaugural Technology Innovation award, sponsored by Clean Harbors. The announcement took
The Warehousing Education and Research Council (WERC), a division of MHI, is pleased to announce the WERC 46th Annual Conference
New orders of manufacturing technology totaled $519.3 million in September 2022, according to the latest U.S. Manufacturing Technology Orders Report
Every small and mid-sized business cares about one thing: a consistent flow of sales. Every time you close a new
An economic slowdown is likely in the next 6 to 12 months with the onset of regular rate hikes. The
Shawn Marken, BDI, has been honored as the 2022 recipient of the PTDA Foundation’s Wendy B. McDonald Woman of the
Holiday spending is expected to be healthy even with recent inflationary challenges, as the National Retail Federation today forecast that holiday
The Power Transmission Distributors Association (PTDA) has named Michael Cinquemani the 31st recipient of its Warren Pike Award for lifetime
NAW urges the government to rein in out-of-control spending The National Association of Wholesaler-Distributors (NAW), which is the voice of
Occupational safety and health professionals create safe work environments in all industries around the globe, helping workers return home safe
The Women In Trucking Association (WIT) has announced Raquel Sanchez as its November 2022 Member of the Month. Sanchez is
The CC-Link Partner Association (CLPA) has welcomed Lattice Semiconductor as the latest member of its network of leading industrial automation
Matt Seaholm, President & CEO of the Plastics Industry Association (PLASTICS) released the statement below in response to a ‘report’ issued
The Women In Trucking Association (WIT) announced the four finalists for the 2022 Influential Woman in Trucking award, sponsored by
Staffing employment held steady in the week of Oct. 10–16, inching up 0.1% to hold at a rounded value of
The Plastics Industry Association (PLASTICS) released its annual Global Trends report today during an executive briefing at the K Show in Düsseldorf,
IMI SalesLeads announced today the September 2022 results for the newly planned capital project spending report for the Industrial Manufacturing
If you have been keeping up with our wonderful economic news you came across comments about Boomers leaving the workforce
“Hi. How are you today?” I hate that line. When salespeople call up and say, How are you today? it’s a warning sign