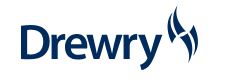
May 2025 World Container Index
For many years, the World Container Index has been the go-to, independent, global reference for index-linked contracts. If your organisation
For many years, the World Container Index has been the go-to, independent, global reference for index-linked contracts. If your organisation
Today, the Association of American Railroads (AAR) reported U.S. rail traffic for the week ending May 3, 2025. This week’s
Felling Trailers Inc. has announced strategic changes to its sales leadership team, appointing Nathan Uphus as Director of Sales and
The Association of American Railroads has reported U.S. rail traffic for the week ending April 26, 2025. For this week,
In this episode of The New Warehouse Podcast, Kevin chats with Brien Downie, President of Holman Logistics, a family-owned third-party
The Association of American Railroads (AAR) has reported U.S. rail traffic for the week ending April 19, 2025. For this
FireLake Manufacturing of Hutchinson, MN, manufactures incinerators and crematoriums, serving the medical, veterinary, and law enforcement sectors. FireLake’s product line
The Association of American Railroads (AAR) has reported U.S. rail traffic for April 12, 2025. For this week, total U.S.
Welcome to this episode of The New Warehouse Podcast, where logistics legend Jim Tompkins, Chairman of Tompkins Ventures, joins the
Anticipated tariffs drive 10th consecutive month of import growth for March Coming off its best first quarter on record, the
The Women In Trucking Association (WIT), Truckstop and Transportation Intermediaries Association (TIA) has announced Martha Payne, transportation attorney at Benesch,
The Association of American Railroads (AAR) has reported U.S. rail traffic for the week ending April 5, 2025. For this
YMX Logistics has announced that Chief Operating Officer Erin Mitchell has been named a 2025 Top Women to Watch in
The Women In Trucking Association (WIT) has announced that WM has continued its Gold Level partnership. The continuation of this
YMX Logistics, a national provider of integrated yard logistics, including gate management, spotting and shuttling services, trailer rentals, and yard management
Today, the Association of American Railroads (AAR) reported U.S. rail traffic for the week ending March 29, 2025. For this week,
The Women In Trucking Association (WIT)has announced Kathy Blaies, a professional carhauler at United Road, as the recipient of the
Trade Tech, Inc., is advancing its Customs capabilities as part of its commitment to supporting freight forwarders and logistics providers
The Association of American Railroads (AAR) has reported U.S. rail traffic for the week ending March 22, 2025. For this
Local leader joins others from around the country in fight to preserve critical infrastructure Local government and law enforcement leaders