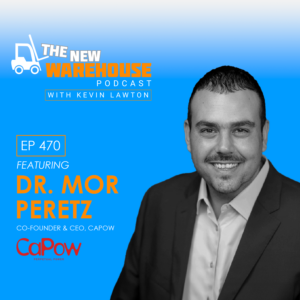
Episode 470: Perpetual Power in warehousing with CaPow
This episode of The New Warehouse Podcast features Dr. Mor Peretz, CEO of CaPow. CaPow, short for capacitive power, is
This episode of The New Warehouse Podcast features Dr. Mor Peretz, CEO of CaPow. CaPow, short for capacitive power, is
By integrating Kardex Shuttles with ZOLLER TMS Tool Management Solutions Software, Intech Athens has taken a monumental leap in streamlining
TrewSort sliding shoe sorter provides retail, e-commerce, and warehouse operations with high-capacity reliable throughput with the added benefits of AI-enabled
This recognition is in the ‘Rising Stars’ category and makes Charles, age 38 from Denver, Colorado, one of only 25
In this episode of The New Warehouse Podcast, Lee Rector, CEO of Embassy Data Logistics, joins Kevin for an informative
It’s an away game for The New Warehouse Podcast as Kevin visits the headquarters of Retail Reworks in Houston, Texas.
Rockwell Automation, Inc. plans to expand its presence at MODEX 2024 in Atlanta, GA., March 11-14. The company will showcase the
Softeon Warehouse Management System (WMS) experts will share the latest in WMS implementations, automated warehousing, and material handling at MODEX
Named the next big winner in the Supply Chain Industry; Clean sweep of both categories – Judge’s Choice and People’s
In this episode of The New Warehouse Podcast, we delve into the transformative power of automation in warehousing and logistics
Booth features the company’s latest forklifts, including new hydrogen fuel cell prototypes From electric and internal combustion machines to new
ABCO Systems LLC announced today its acquisition of FastFetch, known for its best-in-class order fulfillment technologies. This strategic move is set to
Get ready to dive into the intricacies of international e-commerce expansion with guest Riki Hooker, General Manager at Global E-commerce
In this episode of The New Warehouse Podcast, Dennis Hoang, COO and Co-Founder of Patturn, delves into the innovative world
SUN Automation Group, providing innovative solutions to the global corrugated industry, has announced that Amit Nayak has been hired as
In this episode of The New Warehouse Podcast, we had the privilege of visiting Capacity’s headquarters in North Brunswick, New
It’s a common trap that many executives fall into. Consider a company that creates widgets. They must produce the widgets on
Research by SalesLeads’ experienced industrial market research team, shows 369 new planned industrial projects tracked during the month of January.
SalesLeads has announced the January 2024 results for the new planned capital project spending report for the Food and Beverage
Thomson Industries, Inc, a manufacturer of linear motion control solutions, has released a video: ‘Clean and Simple: The Electrification of