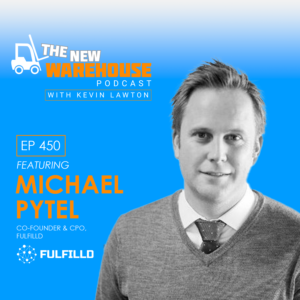
Episode 450: The power of intelligent slotting with Fulfilld
Michael Pytel is the co-founder and CTO of Fulfilld, a pioneering company introducing a new warehouse management system (WMS) to
Michael Pytel is the co-founder and CTO of Fulfilld, a pioneering company introducing a new warehouse management system (WMS) to
In this episode of the New Warehouse Podcast, Anar Mammadov, the Technical Co-Founder of Senpex, shares how Senpex uses artificial
E Tech Group announces the immediate renaming of E-Volve Systems to E Tech Group, following their strategic acquisition on February
In episode 447 of The New Warehouse podcast, Kevin is joined by Glynn LoPresti, the co-founder and CEO of Takt.
52% of companies host enterprise applications in the Cloud; 76% anticipate AI integration in supply chains by 2026 More than
Accolade recognizes Seeq in the “Enterprise Product of the Year” category for its innovative advanced analytics and AI platform for
Steve Denton, CEO of Ware2Go, and Sara Mader, CEO of Palouse Brand, join episode 445 of The New Warehouse Podcast
When considering automated warehousing, stacker cranes have often been the default storage and retrieval choice for pallets and bins. Shuttles,
In the latest episode of The New Warehouse Podcast, Robbie Cluett, Vice President of Business Development & Customer Success at
User benefits include seamless network integration, integrated drive safety, versatility, easy installation and commissioning Siemens is extending its drive portfolio
The International Warehouse Logistics Association (IWLA) recently added two staff members to its education department, bolstering the organization’s commitment to
In episode 441 of The New Warehouse podcast, Kevin is joined by Aaron Alpeter, founder of Izba. Izba, a multifaceted
The New Warehouse podcast recently welcomed Ryan Polakoff, the President of Nexterus, for a fascinating discussion on the evolution and
There’s no escaping it—service delivery is a key business driver and not just for Amazon, but across asset-intensive industries where
In the latest episode of The New Warehouse podcast, Brendan Heegan, Founder and CEO of Boxzooka, joins the show. With
Seagull Scientific, maker of BarTender® software, the global leader in software to print, mark and code labels, RFID tags, products,
Logiwa positions itself not as a traditional WMS but as a modern fulfillment software specifically designed for high-volume, direct-to-consumer operations
In the latest episode of The New Warehouse Podcast, special guest Adam Downing, President of Tryon Solutions, dives into the
When it comes to supply chain and logistics, efficiency takes center stage. Central to this pursuit is the practice of
In the latest episode of The New Warehouse Podcast, Jim Shaw, President and Co-Founder of Zion Solutions Group, joins the