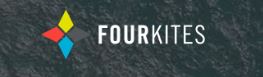
AutoScheduler partners with FourKites to bring visibility to products coming in/out of the warehouse
AutoScheduler Sponsors FourKites Visibility Conference in Chicago, Sept. 6-7th AutoScheduler.AI, an innovative Warehouse Management System (WMS) accelerator, partners with leading