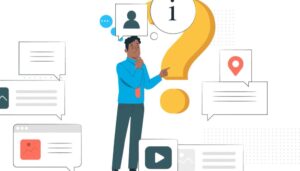
WERC releases 2023 Annual DC Measures Operational Benchmarking Report and online benchmarking tool
The Warehousing Education & Research Council (WERC) has published the 2023 DC Measures Annual Survey and Report and updated the
The Warehousing Education & Research Council (WERC) has published the 2023 DC Measures Annual Survey and Report and updated the
It is now the time of year when many retailers and their supply chain partners will be starting to plan
In this episode of the New Warehouse Podcast, we’re delighted to have Sneha Kumari, Head of Industry Trends at Circular
Jason will provide strategic direction for client automation design and systems integration to transform distribution and fulfillment operations. KPI Solutions
Managing returns has traditionally been treated as an afterthought. But with the rise in eCommerce sales, returns are sure to
Zion Solutions Group is steering the growth of material handling automation amidst evolving economic conditions. With a proven track record
Video surveillance industry leader ships record level of products through May 31 and continues an aggressive growth trajectory Axis Communications,
Distribution center technology provider Lucas Systems announced its rollout of new technologies promising productivity, comfort, and ease of use to
The program will help create a competitive edge for AutoScheduler AutoScheduler.AI, an innovative Warehouse Management System (WMS) accelerator, announces the
The new plant increases the company’s floorspace by 25%, with room for adjacent buildouts to accommodate growth in medical devices
Welcome to a new episode of The New Warehouse! In this episode, we have the pleasure of hosting Connor McGuinness,
Hy-Tek Intralogistics has partnered with Hai Robotics to help reduce customers’ storage footprints, increase workflow efficiency, maximize order pick accuracy,
In the latest episode of The New Warehouse Podcast, Saleh Elhattab, founder and CEO of Gravity, joins Kevin to discuss
The Impact of COVID-19 on Warehouse Real Estate The global pandemic has significantly affected the warehousing industry, with the need
Bastian Solutions, a Toyota Advanced Logistics company, was named a gold winner in the 2023 Edison Awards. The company is
Live from ProMat 2023 Joel Thomas, Director of Intralogistics at Siemens, stops by the booth to discuss the future of
In this episode of the New Warehouse podcast, Corey Apirian, Davinci Micro Fulfillment’s founder, and CEO, sits down with Kevin
Omnicon and Barry Callebaut join forces to revolutionize operations with cutting-edge MES solutions, paving the way for efficient manufacturing and
AMT has appointed Craig Salvalaggio, previously the Chief Operating Officer (COO), as its new president to lead the company’s growth
Leuze is placing its strong growth on a broader footing and has expanded its executive management. Xavier Hamers joined the