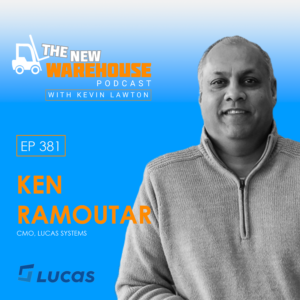
Episode 381: Lucas Systems at ProMat 2023
Ken Ramoutar, Chief Marketing Officer at Lucas Systems, joins The New Warehouse live from ProMat 2023. Lucas Systems is a
Ken Ramoutar, Chief Marketing Officer at Lucas Systems, joins The New Warehouse live from ProMat 2023. Lucas Systems is a
SAKOR Technologies Inc., a recognized leader in the area of high-performance dynamometer systems, announces the release of the DynoLAB™ GenV
CMO Dan Gilmore and CTO Mark Fralick of Softeon join The New Warehouse from ProMat 2023 to discuss the smart
The Tecsys connector will bring rapid, plug-and-play automation connectivity to robotics integration and warehouse automation solutions SVT Robotics, a provider
Vanderlande has announced the appointment of Andrew Manship as its next Chief Executive Officer (CEO). Andrew will take up the
NFI, a provider of North American supply chain solutions, announced that it has acquired SDR Distribution Services, a multichannel provider
Anil Varanasi, CEO and Co-Founder at Meter, joins The New Warehouse to discuss fast, secure, and reliable wireless connectivity for
Warehouses added to the global building stock in 2023 down 35% compared with 2022. 26% of warehouses are expected to
René Schrama joins the executive leadership team to drive growth across the newly-combined organization Peak Technologies, a provider of digital
In this episode of The New Warehouse, Kevin sat down with Matt Fain, CEO of Pop.Capacity. Pop.Capacity is a digital
Brian Kirst, Chief Customer Officer, and Smitha Raphael, Chief Product and Delivery Officer at SnapFulfil join The New Warehouse to
Vinit Pednekar was recently promoted to Global Business Services Distribution Manager at SLB in Houston, Texas (US). Mr. Pednekar is
Tompkins Solutions has announced that Bob Toupin has joined the company as vice president of IT and supply chain technology.
Monadnock Paper Mills, a manufacturer of technical specialty and premium printing and packaging papers, announced that Stephen (Steve) Murphy has
The experts behind leading-edge cloud-based WMS software, SnapFulfil, have unveiled a breakthrough tech solution that orchestrates all automation devices and
Global logistics automation partner, Swisslog has announced that Mario D’Cruz has joined the company as Vice President of Strategy and
FusionPort™ and FusionPort Staging™ can handle up to 550 Bins per hour and feature improved ergonomics for greater productivity AutoStore™,
Craig Henry, US Industry Manager at Siemens, Intralogistics, joins The New Warehouse to discuss some takeaways from 2023 and what
The Intralogistics segment will provide a holistic, systematic approach to materials handling Siemens recently announced the formation of the new
Vanderlande, the global partner for future-proof warehouse solutions, invites ProMat 2023 attendees to learn about the technologies, services, and expertise