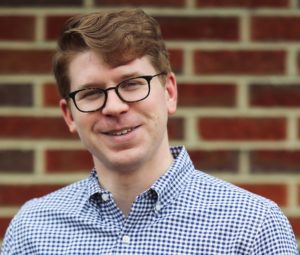
Episode 351: Powerfleet
Scott Walker, VP of Supply Chain Product Management at Powerfleet, joins The New Warehouse podcast to discuss their people-powered IoT
Scott Walker, VP of Supply Chain Product Management at Powerfleet, joins The New Warehouse podcast to discuss their people-powered IoT
The New Warehouse welcomes fellow podcasters Dan Coll and Ninaad Acharya to the show to discuss their backgrounds and how
Tompkins Solutions, a supply chain consulting and material handling integration firm, today announced that Billy Carter has joined the company as
The New Warehouse podcast is excited to welcome Kristin Toth, the president and COO of Fernish. Fernish is a unique
VRCs help maximize existing space, while also costing less than dealership expansion It’s no surprise that constructing a new dealership
Hy-Tek Holdings (Hy-Tek), a portfolio company of Dunes Point Capital, LP (DPC), has acquired Winchester Industrial Controls LLC (“Winchester”). Winchester,
The Warehousing Education & Research Council (WERC) announces the availability of a new warehousing e-learning course, called Distribution Logistics Fundamentals.
The New Warehouse welcomes Tony Ingham, Product Owner at Fulfilld, for our first podcast of 2023. Fulfilld is a leading
PeakLogix announced that Pat Peplowski has joined the company as VP of Business Development. Peplowski is a data-driven leader who
Carlisle Companies Incorporated has announced a commitment to achieve Net-Zero greenhouse gas emissions across its entire value chain by 2050.
This week’s episode of The New Warehouse brings you John O’Kelly, President and Founder of Newcastle Systems. Newcastle Systems provides
IMI SalesLeads announced the November 2022 results for the newly planned capital project spending report for the Industrial Manufacturing industry.
Nucor Warehouse Systems (NWS) has promoted Reed Reynolds to Commercial Director effective Jan.1, 2023. In this new position, he will
CEO and founder of HomeRoots, Gil Bar-Lev joins this week’s episode of The New Warehouse to discuss offering a business-to-business
LMI® at 53.6 Growth is INCREASING AT AN INCREASING RATE for: NOTHING Growth is INCREASING AT A DECREASING RATE for:
JLT Mobile Computers, a developer of reliable computing solutions for demanding environments, has launched JLT Insights, a new data-driven software dashboard for industries with warehouses.
The transformational electronic platform provides speed and security The International Group of P&I Clubs (the Group) added Secro as an
Virtual training is designed to increase product knowledge among installing technicians and salespeople, including Dec. 9 educational webinar about the
Plan to increase production by up to 60 percent KION Warehouse Systems (KWS) company premises are to be expanded by at
If you want to scale your business or add tools to your warehouse, you will want to tune in to