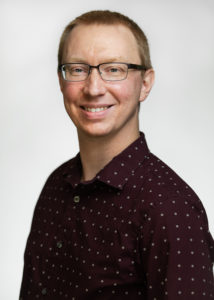
Westfalia promotes Alex Eisenhart to Manager of Business Solutions
In his new role, the former Solutions Architect will lead internal business process development, and data quality management, and oversee
In his new role, the former Solutions Architect will lead internal business process development, and data quality management, and oversee
Welcome to The New Warehouse podcast. In this episode, Kevin is joined by John Evans, Sr. Customer Success Manager/3PL Team
Acquisition of four generation Maryland-based loading dock specialist supports Miner’s industry expertise and nationwide reach Miner Ltd., the dock and
LEDtronics® Inc. has announced its newest series of UL-listed LED Post Top Lamps that put out an impressive amount of
Live demo of Energy Management & Equipment Uptime Solutions at IMTS and AEE World tradeshows Synapse Wireless, Inc., an Internet
The New West Coast office enhances the company’s national presence for warehouse optimization and automation services MHS Lift, Inc., a
TA Services, a full-service 3PL (third-party logistics) provider, has announced that it has been included in SupplyChainBrain‘s list of 100
TrueSource, an OnPoint Group Company and the national leader in critical facility maintenance for retailers and property managers announced the
Coming to you from the booth at MODEX 2022, we welcome Jonathan Katz to this week’s episode of the New
Euan Finlay brings 25 years of driving operational excellence Brown and Caldwell just announced that Euan Finlay has been promoted
AutoScheduler.AI, an innovative Warehouse Management System (WMS) accelerator, names Keith Moore as CEO with Tom Moore, Founder, moving to the Board of
Numina Group’s key services, design engineering, and software-driven warehouse automation integration remain in high demand as manufacturers and distribution operations
Duravant welcomes Chad E. Walker to the position of Senior Vice President and General Counsel. In this role, Walker will
In this week’s episode of The New Warehouse, we are talking about an often overlooked aspect of warehousing, yard management
Synergy North America has been retained on the elite Gartner Magic Quadrant (MQ) for Warehouse Management Systems (WMS) – for
Concentric, LLC, the national provider in DC power management and maintenance for the material handling and critical power industries, announced
How fitting to have three guests join me for what is officially the 300th episode of The New Warehouse Podcast.
Further strengthening KPI’s capacity and expertise to provide end-to-end distribution solutions for clients KPI Integrated Solutions, a supply chain consulting,
SalesLeads has announced the June 2022 results for the newly planned capital project spending report for the Industrial Manufacturing industry.
The Northeast US premier material handling company marks a major business milestone, building on one hundred years of dedication, professionalism,