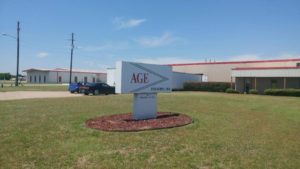
Rethinking Supply Chain Management
The supply chain crisis continues to place enormous strains on business. Global trade has been knocked out of balance. COVID-19
The supply chain crisis continues to place enormous strains on business. Global trade has been knocked out of balance. COVID-19
New Insights From Lucas Systems ‘Voice of the Warehouse Worker’ Market Study Warehouse workers value technology so much that they are
Recognized for the second time for the Warehouse Resource Optimization category AutoScheduler.AI, an innovative Warehouse Management System (WMS) accelerator, announces the company
WMS technology innovator Synergy Logistics celebrates 50 years in business One of the world’s pioneers of cloud-based warehouse management software,
The Warehousing Education & Research Council (WERC) recently announced the availability of the 2022 DC Measures report. DC Measures captures
LMI® at 65.0 Growth is INCREASING AT AN INCREASING RATE for Inventory Levels Growth is INCREASING AT A DECREASING RATE
Johnson Controls and Accenture will deliver two new Johnson Controls OpenBlue Innovation Centers seeding further development of AI-enabled building control
The Tranzonic Companies, a respected manufacturer of cleaning, maintenance, and personal protection products, has named Chris Adams its new vice
Association for Advancing Automation expands floor space for Automate 2023 after this year’s show ends with 24,000 registrants, 600 exhibitors,
AutoScheduler.AI, an innovative Warehouse Management System (WMS) accelerator, has been named to the American Journal of Transportation (AJOT) Top 50 Logistics Tech Provider
Norman Tu, CEO and Founder of DCL Logistics, and his sons Dave and Brian Tu joined me on this week’s special Father’s
Caja Robotics, a provider of robotic and flexible goods-to-person solutions in fulfillment, engages in close cooperation with Fives, one of
Global transport and logistics provider GEODIS and KNAPP, a technology partner for intelligent value chains, have announced a new collaboration
In this episode, I was joined by Mark Zabloudil and Matt Warner representing Alpine Supply Chain Solutions as their customers.
In this episode, I was joined by Justin Warren and Don Gilbreath of Rajant at MODEX 2022. Rajant provides kinetic
Warehouse Management and Warehouse Execution Systems deliver throughput, Operating Cost Reduction, and ROI Softeon, a global supply chain software provider
The Port of Long Beach announced that Amazon Web Services, Inc., an Amazon.com, Inc. company, will be used to power
In this episode, I was joined by Pat Hoskins of Newcastle Systems at MODEX 2022. Newcastle Systems is focused on
BeerBoard a provider of technology and automated business intelligence for the on-premise retail industry has announced that Josh Solomon has been
Kyocera Document Solutions America, Inc. has announced the appointment of Joseph Fuccillo as Vice President of Software & ICT, and