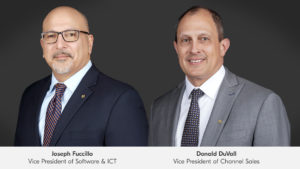
Kyocera strengthens its leadership team with the addition of new Vice Presidents of Software & ICT and Channel Sales
Kyocera Document Solutions America, Inc. has announced the appointment of Joseph Fuccillo as Vice President of Software & ICT, and
Kyocera Document Solutions America, Inc. has announced the appointment of Joseph Fuccillo as Vice President of Software & ICT, and
Concentric, LLC, a national provider in DC power management and on-site maintenance for the material handling and critical power industries,
SRSI (Slate River Systems, Inc.) and Dematic signed an integrator relationship agreement. SRSI will now be a certified integrator of
An online farmer-to-farmer and Ag tech company has fast-tracked its expansion plans thanks to a tailored ‘Self Implementation’ program from
Seeq Corporation, a provider of manufacturing and industrial internet of things advanced analytics software, launched Conneqt, the company’s expanded global
On this episode, I was joined by Mike Stein of Signode at MODEX 2022. I first spoke to Signode at
Co-Founder of LeanLogistics, Jeff Potts, brings 30 years of experience to empower the company for growth and greater profitability AutoScheduler.AI, an
In this episode, I was joined by the father-daughter duo of Dave and Maddie Haley. They are both in the
In this episode, I was joined by the President of Verses, James Hendrickson, at MODEX 2022. James and I reconnected
False alarms drain the life out of security operations on so many levels by wasting valuable personnel resources and budget
WMS technology innovator, Synergy North America Inc, has further enhanced its multiple billing software that already offers the highest levels
Warehouse automation company, AutoStore, just announced the opening of its new Singapore office. The location will serve as the local
AFFLINK LLC, a global provider in supply chain management, announces the appointment of Todd Gatzulis as Senior Vice President of
MHS Global (“MHS”), a global provider of material handling automation technology and systems integration, and Fortna (“Fortna”), a software and
In this episode, I was joined by Dave Haley of Open Sky Group at MODEX 2022. Open Sky Group is
The latest release of AMS Machine Works enables holistic condition monitoring programs for critical assets Global software and technology provider
What is a demand-driven enterprise? The Demand Driven Institute defines it as one that “can sense market changes, adapt to complex and
On this episode, I put on my other hat which is Professor Lawton, and was joined by previous guest Jeff
The new WISER ATLAS provides revolutionary WISER Locator precision and ease of use scaled to thousands of work orders/assets across
On this episode, I was joined by the Director of E-commerce Operations & Fulfillment at Bonnie Plants, Sid Phelps. Bonnie