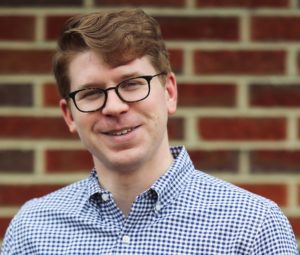
EP 263: Bonnie Plants
On this episode, I was joined by the Director of E-commerce Operations & Fulfillment at Bonnie Plants, Sid Phelps. Bonnie
On this episode, I was joined by the Director of E-commerce Operations & Fulfillment at Bonnie Plants, Sid Phelps. Bonnie
EnerSys®, a global provider in stored energy solutions for industrial applications, will feature its family of virtually maintenance-free NexSys® battery
Siemens is presenting its latest solutions for smart and networked drive technology. By networking entire drive systems, machine and plant
In this episode, I was joined by two Ryan’s both from Phantom Auto. Ryan Chesterfield and Ryan Clifford both work
Three years of The New Warehouse Podcast! I can hardly believe it but I’m taking a moment to celebrate all
BeerBoard, a provider in technology and automated intelligence for the on-premise hospitality industry, announced that Florida Distributing Company (FDC), which
Synapse WMS to power warehouse operations for leading national third-party logistics provider Zethcon Corporation announces the selection of the company’s
On this episode, I was joined by the previous guest Justin Griffith of StayLinked. Justin is the CTO at StayLinked
Aptean, a global provider of mission-critical enterprise software solutions, announced the launch of Aptean EAM, an all-new, cloud-based enterprise asset
In this episode, I share my own knowledge from experience on how to increase your warehouse education. I have been
Unlike vendors with multiple WMS products, Softeon Warehouse Management System serves large, mid-level, and smaller operations across a fulfillment network
On this episode, I was joined by the US Regional Sales Director at JLT Mobile Computers, Glenn Lundgren. JLT Mobile
In this episode, I discuss something very important in the warehouse, cleaning! This is an incredibly important part of maintaining
WMS technology innovator, SnapFulfil, selects Brian Kirst a seasoned 3PL Executive for the role of US Vice President Sales &
Renowned Retail, CPG, and Supply Chain Veteran brings a world-class track record to a global provider of Internet of Things
Jeff Born has been named as the director of procurement and supply chain solutions overseeing North American activities for Tubelite Inc., Alumicor
The National Association of Wholesaler-Distributors (NAW) just announced the winners of its inaugural Distributors Deliver Award given at last week’s
Connected Industrial Mobility provider, SIERA.AI, announced the completion of a $6.8 million-dollar seed funding round. The funding round was supported
Hikvision, a manufacturer and supplier of security products and solutions, continues to build on its popular line of AcuSense surveillance
The current global trade crisis has highlighted weaknesses within the supply chain and forced the industry to assess, evolve, and