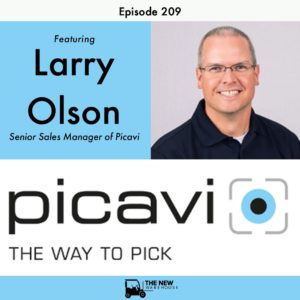
Larry Olson of Picavi featured in Material Handling Wholesaler
Larry Olson, Senior Sales Manager at Picavi, the provider in pick-by-vision technology, was recently interviewed by Kevin Lawton, podcast host
Larry Olson, Senior Sales Manager at Picavi, the provider in pick-by-vision technology, was recently interviewed by Kevin Lawton, podcast host
SalesLeads just announced the August 2021 results for the newly planned capital project spending report for the Industrial Manufacturing industry.
SalesLeads has announced the August 2021 results for the newly planned capital project spending report for the Distribution and Supply
GEODIS, a global transport and logistics provider, and Advanced Handling Systems (AHS, LLC), a full-service provider of integrated fulfillment and
On this episode, I was joined by Brad Wright of Chunker. Brad is the CEO and Founder of Chunker which
Gamber-Johnson has announced the availability of six new protective handheld technology docking cradles to support the popular Zebra TC5X and
On this episode, I was joined by the Senior Sales Manager at Picavi, Larry Olson. You may remember Picavi from
On this episode, I was joined by the Co-Founder and Group CEO of Hatio, Bernard Hor. Hatio is a Southeast
Zethcon Corporation, a provider of warehouse software for 3PL providers, announces the latest standard release of its flagship product, Synapse
On this episode, I was joined by Adam Gershenson of NutraScience Labs. Adam is the Director of Logistics & Fulfillment
Members of the International Warehouse Logistics Association (IWLA), the resource for warehouse logistics, recently elected Jeremy Van Puffelen, vice president
As the only trade association focused on the third-party warehouse logistics industry, the International Warehouse Logistics Association announces its newest educational course:
Last month we were discussing the finer points of the Service CX (customer experience). As I pointed out in the
New Jersey Exec named Chairman of the Board Members of the International Warehouse Logistics Association (IWLA), the resource for warehouse
In this year’s report, we break down the challenges of managing disruption into three major phases: Respond, Recover, and Thrive. Each explores
On this episode, I was joined by the VP of Product and Analytics at 6 River Systems, Gillan Hawkes. I
REMIRA sticks to its strategic expansion course: One week after the purchase of Nicando Software GmbH, the company also acquires
Members of the International Warehouse Logistics Association (IWLA) recently elected Scott Mayfield, president & CAO Kenco Logistic Services, Chattanooga, Tenn.,
SolaHD SDU AC-B offers optional network communications for advanced control and diagnostics As more power-sensitive devices are deployed in automated
EP 176: CognitOps On this episode, I was joined by the Co-Founder & CEO at CognitOps, Alex Ramirez. CognitOps is