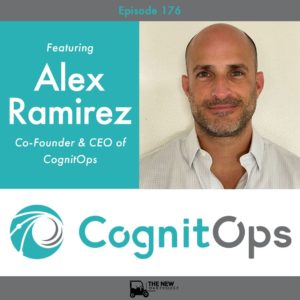
EP 176: CognitOps
EP 176: CognitOps On this episode, I was joined by the Co-Founder & CEO at CognitOps, Alex Ramirez. CognitOps is
EP 176: CognitOps On this episode, I was joined by the Co-Founder & CEO at CognitOps, Alex Ramirez. CognitOps is
In this episode, I was joined by John Wirthlin of Zebra Technologies to discuss RTLS. John is the Industry Principal
In this episode, I was joined by Dan Gilmore who is the Chief Marketing Officer at Softeon. A supply chain
In this episode, I was joined by the CTO of StayLinked, Justin Griffith. StayLinked is a terminal emulation solution that
On this episode, I was joined by the VP and Head of Product at KINETIC, Chris Kuruc. KINETIC is a
Softeon, a global supply chain software provider with the industry’s best track record of customer success, will feature a number
Comprised of the drive, motor, and gearbox, this new distributed drive system is available as a complete solution for motor-mounted
The company will highlight intralogistics solutions with innovative digital demonstrations at the first virtual ProMat DX trade show The Raymond Corporation will
On this episode, I was joined by the number one contender for most guest spots, Fergal Glynn of 6 River
After 25 years in business, JLT Mobile Computers, a supplier of reliable computers for demanding environments, is making available the benefits
Alliance brings pre-validated hardware/software solutions for easy, error-free installations that increase efficiency, productivity and security in logistics and warehousing JLT
With the significant growth in e-commerce, the market potential for third-party logistics services is growing rapidly across the world. In
Developed by Servotronix with an EtherNet/IP interface from STXI Motion, the softMC compact microcontroller enables any major OEM programmable logic
The AutoScheduler.ai, an innovative Warehouse Management System (WMS) accelerator, announces that two executives, Thomas A. Moore, Founder and CEO, and
The test center located in Karmøy, Norway, can replicate hot and cold weather conditions as well as simulate earthquakes AutoStore,
Advanced Handling Systems (AHS, LLC) has announced that they have been contracted by Gap Inc. to design and integrate an Exotec Skypod
In this episode, I was joined by the Co-Founder & CTO of Fulfilld, Michael Pytel. Fulfilld is a new warehouse
The modernized Customer Experience Center will feature state-of-the-art fulfillment technology and automation to support Old Navy’s growing online business Gap
The supply chain industry is evolving to enable and sustain the rapid demand for goods and services globally. The competitive
The Rufus RADD™ Tab delivers increased visibility into warehouse operations and can be used on warehouse forklifts and vehicles Rufus