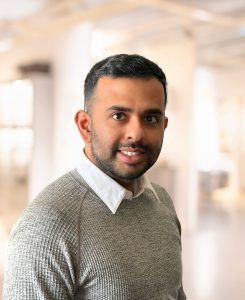
AI-powered robotics are reshaping the warehouse floor
Robots in warehouses aren’t a novelty, but with the infusion of AI, they’re becoming integral players in operations. These intelligent
Robots in warehouses aren’t a novelty, but with the infusion of AI, they’re becoming integral players in operations. These intelligent
Storage Solutions (SSI) has announced a new logo and yellow brand identity at ProMat 2025. Storage Solutions, a Jungheinrich Company,
The world of logistics is changing fast, and nowhere is that more evident than in retail return logistics. In this
Bradford Systems has announced a strategic partnership with Rainbow Dynamics. This collaboration aims to revolutionize storage and retrieval systems across
Experience All Your Automation on One Platform at Mujin’s Booth #N6733 and Engage Hands-On in the MujinOS Experience Center Mujin
Advanced Intralogistics will showcase the latest innovations in automation technology at ProMat 2025, which is taking place March 17-20 at
Appearing at ProMat 2025, a manufacturing and supply chain show, next week, Kardex Solutions and Paccurate have announced a strategic
In this episode of The New Warehouse Podcast, Kevin sits down with Andre Luecht, Global Strategy Lead at Zebra Technologies;
Welcome to this episode of The New Warehouse Podcast featuring Jackie Wu, Founder and CEO of Corvus Robotics. Corvus Robotics
Users can query logistics operation data, create reports, and generate dashboards via chat. Requests such as releasing orders or unblocking
In this episode of The New Warehouse Podcast, Kevin welcomes Pascal Jetté, VP of Business Development at GMR Safety. They
MHS Lift, Inc., a provider of warehousing and distribution solutions across North America, has been recognized as a UniCarriers Premier Club
In this episode of The New Warehouse Podcast, Kevin speaks with Wanda Riddick Johnson, Supply Chain Technology Fellow at Deloitte. She
To strengthen market leadership and scale global growth Verity, an AI-powered mobile intelligence that enables complete warehouse operational visibility through
Attendees to learn how to enhance their operations at booth #S2303 Dematic, a global leader in supply chain automation, will
Welcome to another episode of The New Warehouse Podcast, where we dive into a unique solution for evaluating warehouse employee
The world of warehouse automation is evolving rapidly, but one persistent challenge remains: transparency. Many businesses looking to implement automation
Versatile portable cooling unit revolutionizes temperature-controlled storage for warehousing needs Amerikooler, a commercial refrigeration solution, has announced the launch of
This growth will further Wize Solutions’ plans for the Phoenix Metro Area Wize Solutions has announced that it has acquired
Picture a bustling warehouse during the holiday season, with workers racing against time to fulfill an avalanche of online orders.