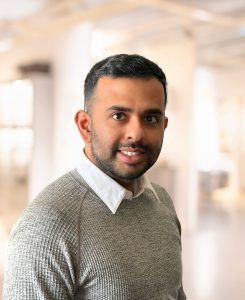
AI in warehousing: Revolutionizing labor efficiency and workforce dynamics
Picture a bustling warehouse during the holiday season, with workers racing against time to fulfill an avalanche of online orders.
Picture a bustling warehouse during the holiday season, with workers racing against time to fulfill an avalanche of online orders.
E-commerce growth has transformed how brands approach logistics, fulfillment, and omnichannel distribution. In this episode of The New Warehouse Podcast,
On The New Warehouse Podcast, Kevin sits down with Oda Bolden. Oda is the Director of Supply Chain Network, RSD(Radiology,
On The New Warehouse Podcast episode, Kevin welcomes Troy Strawhecker, Chief Strategy Officer and Partner at JT Logistics. Based in
On this episode of The New Warehouse Podcast, Kevin is on-site at Zebra Technologies’ robotics demo center in San Jose,
As part of its continued commitment to strengthening its Americas leadership team, supply chain, and automation solutions provider, Dematic announces the
Zion Solutions Group has announced its third consecutive win of the Most Valuable Partner (MVP) Award from the Material Handling
The latest episode of The New Warehouse Podcast welcomes back Brian Tu, Chief Revenue Officer, and Dave Tu, President of
The labor challenges in warehousing persist, with shortages and inefficiencies making it difficult for companies to find and retain reliable
This episode of The New Warehouse Podcast features Anthony Jules, Co-Founder and CEO of Robust AI. Anthony shares insights into
Distribution center technology provider, Lucas Systems, has announced its new software enhancements to help warehouses make quicker and more effective
Today’s episode of The New Warehouse Podcast features returning guest Mike Myers, now the founder of Lully AI. A seasoned
Let’s step into a warehouse during the holiday rush hour. Orders are flooding in, inventory is off shelves, and workers
The imminent end of hard stamping means much more than avoiding damage to the product, says Andy Charlesworth and Richard
Welcome to this episode of The New Warehouse Podcast! Kevin catches up with Joe McIntyre, the general manager at Slotted,
ReposiTrak and Upshop have announced a global partnership to integrate their technology platforms, connecting traceability data from the supply chain
Keith Frymark, Senior Vice President of Supply Chain and Quality at Seed Health, joins The New Warehouse Podcast to discuss
Welcome to this episode of The New Warehouse Podcast, featuring Macon Stokes, CEO of Amplifier. Amplifier, a 3PL provider based
KPI Solutions (KPI), a supply chain consulting, software, systems integration, and automation supplier, announced that Gartner has recognized the company
On this episode of The New Warehouse Podcast, Tyler Wiard, Director of Strategic Partnerships at Candor Expedite, shares insights on