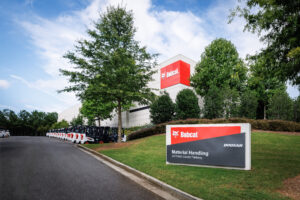
Bobcat celebrates $3.26M renovation at Buford facility
Bobcat Company recently brought material handling into the Bobcat brand, transitioning from Doosan Industrial Vehicle to Bobcat in early 2024.
Bobcat Company recently brought material handling into the Bobcat brand, transitioning from Doosan Industrial Vehicle to Bobcat in early 2024.
Today’s episode of The New Warehouse Podcast features Bobby McKinnon, Co-Founder and CEO of Deliverlitics. Deliverlitics is dedicated to solving
With systems integration partner KPI Solutions, Kenco’s new automated storage and retrieval system will shorten click-to-delivery times for the 3PL’s
Cimcorp’s automation boosts storage capacity and enhances operational efficiency, helping the Finnish brewery handle growing production volumes and seasonal demands
Today, Mike Robinson, the Head of Retail Solutions and a founding member of The Eighth Notch, joins the show to
Welcome to another episode of The New Warehouse Podcast! Today, Jason Tham, co-founder and CEO of Nulogy, joins the show
Kito Crosby, a global leader in the lifting and securement industry, proudly announces the completion of a major investment at
The sustainable accessories manufacturer expects to double its sales amidst the expansion of an industry set to reach $500 billion
The New Warehouse Podcast episode features Christian Rognes, the Chief Product Officer at Element Logic. Element Logic is the first
The Most Robust, Cost-Effective, and Easy-to-Install Piping System Available, for Pressures up to 1015 PSI Unipipe Solutions, an industrial piping
Welcome to The New Warehouse Podcast! In this episode, we dive into the world of coffee with a mission. Our
The distribution process is burdened with consumer expectations demanding faster deliveries, warehouse labor shortages, scarcity of physical storage space, and
Supply chain leaders are turning to automation and AI to enhance operational efficiency, reduce costs, and elevate the customer experience
Distribution center technology provider Lucas Systems announced its next generation of Dynamic Slotting, a warehouse game changer for making in-the-moment
Investment to speed technology advancement and accelerate growth AutoScheduler.AI, an innovative Warehouse Orchestration Platform, and WMS accelerator announces a $6.5M
The New Warehouse, with host Kevin Lawton, will host a special LIVE LinkedIn podcast with the authors of The Warehouse Revolution—Automate or Terminate at
Company launches first automated tool for document management Freightmate Ai announced that it has secured a pre-seed funding round led
In the latest episode of The New Warehouse Podcast, Kevin chats with Erik Nieves, CEO of Plus One Robotics. The
In a groundbreaking move set to enhance and redefine warehouse operations, Zion Solutions Group has announced its strategic partnership with
Easy-to-use tools help companies with less complex and smaller operations NetLogistik, a provider of transformative services for supply chain digitalization,