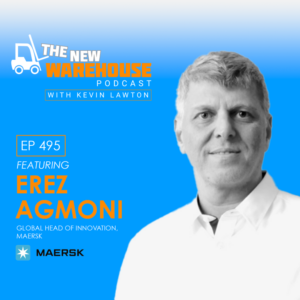
Episode 495: End-to-end supply chain innovation with Maersk
This episode of The New Warehouse Podcast broadcasts live from the Maersk Podcast Studio at Manifest. Erez Agmoni, Global Head
This episode of The New Warehouse Podcast broadcasts live from the Maersk Podcast Studio at Manifest. Erez Agmoni, Global Head
Oren to drive strategic sales efforts for Dematic Americas with two decades of leadership experience Further strengthening America’s leadership team, Dematic
Swisslog, a provider of best-in-class warehouse automation and software, has announced it is opening a new Americas region headquarters in
Supply chains are investing in technologies to accelerate resilience, agility, and flexibility to better navigate current and future disruption The
First-of-its-kind research shows productivity and profitability loss caused by ‘dropped sessions’ StayLinked’s research report, titled ‘Dropped Sessions – The Hidden
Nucor Corporation announced it has agreed to acquire Rytec Corporation, a manufacturer and seller of high-speed, high-performance commercial doors. The all-cash
On this bonus episode of the podcast, we are talking AI in the warehouse with Ravi Maganti from Manhattan Associates.
For the sixth consecutive year. In a dynamic market where AI and the Cloud reign supreme, Generix reaffirms its commitment
In episode 490 of The New Warehouse Podcast, Steve Hopper, founder and principal of Inviscid Consulting, joins the show to
In episode 489 of The New Warehouse podcast, Mark Stanton, President and General Manager of Elokon Group, joins to discuss
The award recognizes top companies in the Greater Cincinnati region based on employee feedback. Trew, LLC has been recognized as
The New Warehouse Podcast welcomes Carson Menke, Regional Sales Manager, and Brian Markison, Director of Sales, from Rocrich AGV Solutions.
The German Design Council has honored LEIBINGER’s innovative, high-performance industrial printer, IQJET, with the Gold German Innovation Award on May
For the fifth consecutive year, MHS Lift, Inc. has been honored as one of the 2024 Top Workplaces in the Greater Philadelphia
Episode 487 takes The New Warehouse Podcast on the road to the heart of industrial innovation at the Nucor Warehouse
Peak Technologies has announced a significant milestone, becoming a certified Zebra Technologies partner in Australia, delivering fixed industrial scanning solutions
Welcome to The New Warehouse Podcast, where we delve into the evolving world of logistics and automation. We’re joined by
Brian previously looked after all customer-facing elements of the business in North America, but now oversees all aspects of Sales,
Nucor Corporation has announced that Executive Vice President Douglas J. Jellison plans to retire on June 8, 2024 after more
The Plastics Industry Association (PLASTICS) released its 2024 Bioplastics Market Watch Report today during an education session at NPE2024: The Plastics