The imminent end of hard stamping means much more than avoiding damage to the product, says Andy Charlesworth and Richard Oldknow, of YOKE Industrial Corp.
We all know what hard stamping is: a type of punch that, when struck, creates an indentation on the surface of the product that can be read or understood by the item’s user.
It is about as far from state-of-the-art as you can get and, in an industry embracing the Internet of Things (IoT), Artificial Intelligence (AI), Blockchain, automation, the metaverse, etc., it’s remarkable that hard stamping remains so prevalent. We continue to visit rigging shops and see people at workbenches hard stamping batches of 1,000 shackles and preparing the individual certification that needs to be produced.
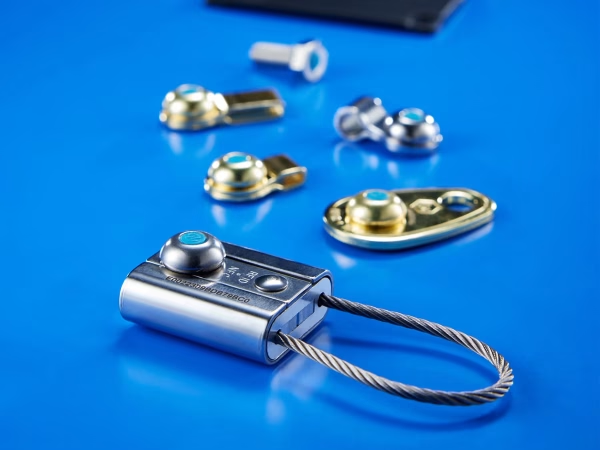
The major problems associated with this traditional type of marking product include:
- Time involved with hard stamping and paperwork.
- Potential damage it causes; without clear guidance on where to stamp or what tooling to use, it is possible to introduce stress raisers into the product, making it more susceptible to premature failure.
- Hard to read markings.
- A lack of control over font sizes and sharp-edge fronts.
There is also a large volume of equipment in the industry that is marked with color-coded tie wraps that give a visible indication that the item is within its six-monthly examination period. However, that doesn’t mean that the item has been given its pre-use inspection.
The wider problems associated with stamping and tagging begin to emerge, meaning that a wholesale move towards radio frequency identification (RFID) and Software as a Service (SaaS) can’t come soon enough — with pre-use checks, unique identification numbers, and the Machinery Regulation all at the fore of the revolution led by YOKE Industrial Corp.
To back up that claim, YOKE had a decision to make a few years ago. We could have taken one or two RFID-equipped products and introduced them to the industry to assess potential uptake, or fully digitalize our complete range, where size permitted, and state our intentions to change the way the industry works tomorrow. We chose the second option — and have never looked back.
Aligned with a mission to manufacture quality rigging and safety equipment to deliver superior safety protection, RFID drastically enhances safety and helps the industry keep up with pre-use checks, unique identification numbers, and the move toward January 2027, when everybody is expected to be working to the Machinery Regulation.
That’s when the EU Machinery Regulation fully applies, and the Machinery Directive 2006/42/EC is repealed. Eventually, the Machinery Regulation will eliminate all the different requirements across all of the EU member states, so they all follow the same regulation.
One of the most significant changes is the inclusion of original certifications and manuals to be supplied digitally with products. As the world moves towards a more environmentally friendly future, we are certain that by digitalizing our full range of products, we are removing the need for any paper trail as the product will carry the history from initial supply through its lifetime of use.
What are the chips and how do they work?
RFID has been used for many years in industries such as agriculture, where cattle are tagged, for example, but it was always difficult to incorporate it into rigging due to the complexities of manufacture and ensuring suitability for items where they can last decades if used properly.
With the additional work YOKE has carried out with Near Field Communication (NFC) technology, it means that today every user with a mobile phone capable of paying a bill now also has the ability to at least check a component for safe use instruction.
Already, several original equipment manufacturers (OEMs) are using BlueSupra. Put simply, BlueSupra is the brand name for the range of tags we produce and SupraNano is the encased NFC RFID chip. For YOKE products, we pressure-fit the SupraNano directly into the steel, but for items such as a snatch block, we utilize a retrofit tag to permanently attach it.
The equipment is extremely durable. Our BlueSupra retrofit tags are put through a series of tests covering impact and wear and the SupraNano is subjected to rigorous temperature (-30 / +125 degrees C) and water ingress (6,000m subsea) tests.
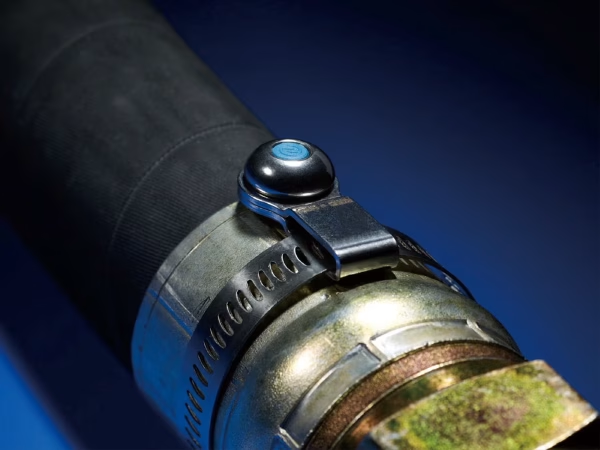
YOKE’s RFID chips are even in a 7mm connector and 1t capacity shackle. Using software from RiConnect, a SaaS provider, they can be read even on a regular smartphone or device, providing information not only like the unique identification number, but also a full description, brand name, registration date, status, documentation, and any asset number or other serial number if added by the distributor. We even supply these tags to competitors, removing any barriers where some manufacturers do not yet add the digital chip to their products.
The industry is thusly harnessing all the inherent benefits of the technology and, importantly, doing so in line with the Lifting Equipment Engineers Association’s (LEEA) ongoing guidance and industry standards. Consider how the duty holder gains too. While supply legislation does not require a manufacturer of lifting equipment to give it a unique identification — it simply requires them to mark one on the product if they have specified one — user legislation requires the duty holder to have lifting equipment inspected and/or thoroughly examined and issued with a report of that inspection or thorough examination. This report must identify the equipment without ambiguity so that defects can be remedied efficiently.
We frequently point people to LEEA’s guidance that where a duty holder has many items of a similar generic form of lifting equipment, it is considered best practice to give each piece its unique identification number, which is then recorded on each thorough examination report, thus ensuring the report is traceable to the equipment without ambiguity.
All this can be achieved with RFID and SaaS — without hard stamping or color-coded tie-wraps. Hard stamping is not a favorable way to identify equipment; it can bring inherent damage, and logistical and inspection issues thereafter. Each inspector will inspect hundreds of thousands of items in their lifetime, cleaning off dirt and mud, just to be able to read the hard stamp. This can lead to mistakes as numbers and letters are not always readable.
Most inspection companies have transitioned away from pen-and-paper systems and equipped their inspectors with smartphones or tablets, so they do not want to be working in the mud with wire brushes trying to read hard-stamped markings. It is expensive and not time-efficient when the technology is readily available in their hands.
Imagine never having to stamp a shackle or a sling tag ever again.